Is My Dew Pointer Measuring Correctly?
Watch the video to learn about important factors for consistent and accurate measuring of a dew point in a furnace.
Typical Installation with the Air Products' Dew Point Monitoring System
The Air Products’ dew point monitoring solution enables sampling hot-zone atmosphere using a sampling pump.
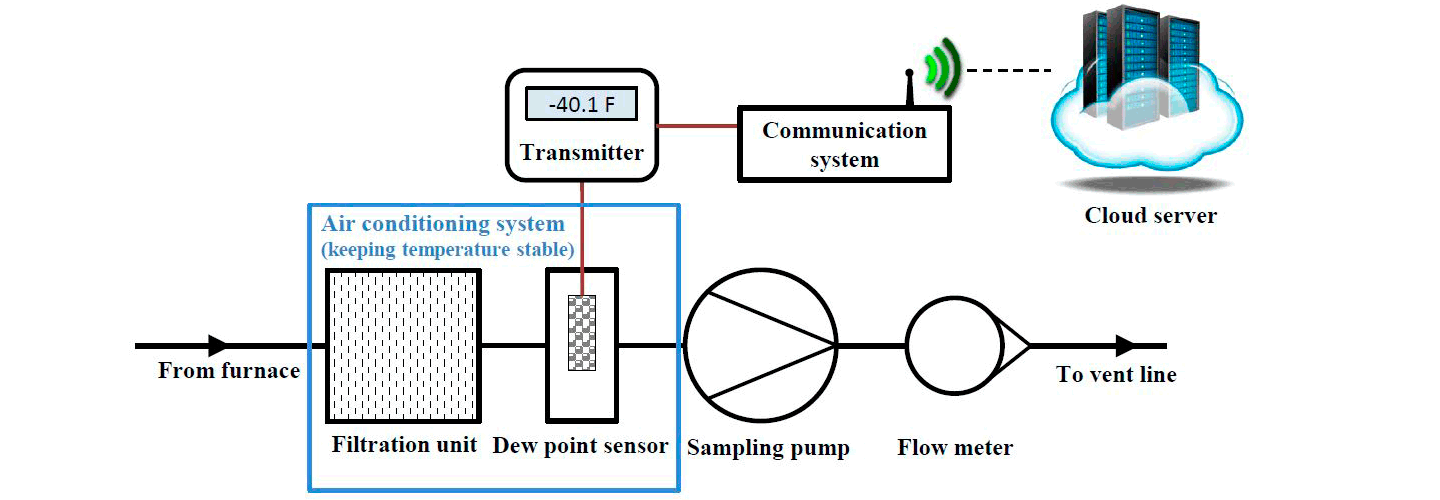
Learn more about our Dew Point Monitoring System
Schedule a free consultation with one of our metals processing experts.
Ask the Expert

Don Bowe
Applications Engineer
“Is my dewpointer measuring correctly?”
Dew point (DP) is a measure of the moisture composition in a furnace atmosphere. In the various zones of a sintering furnace, the atmosphere can vary widely from a relatively wet, oxidizing atmosphere in the pre-heat zone to a dry, reducing atmosphere in the hot and cooling zones. Maintaining the appropriate atmosphere composition in each zone is critical to achieving the desired delubrication and consistency of the sintered product.
Dew points of –35 to –45°C (–31 to –49°F) are typically desired in the hot zone to ensure carbon control and a good sinter. Continuous monitoring of the dew point in the hot zone can be challenging. Particulate and vapor-phase contaminants in the sample gas stream can potentially accumulate in filtering systems and on sensors. As a result, dew point readings can drift significantly, causing erroneous measurement and necessitating frequent cleaning, recalibration, and sensor replacement. Temperature variations within the sampling unit can also impact the accuracy of the sensors.
These issues can be mitigated by incorporating an automated self-cleaning and sensor calibration process. Temperature control of the sensor and the sampling system are also essential to maintain consistency. This can be achieved via various design features. Drifts and changes in dew point that are reported through local monitoring/alarms or remotely through cloud server access can also help to address furnace operational issues quickly and efficiently.
Continuous dew point monitoring helps manufacturers comply with CQI-9 and NADCAP requirements, and enables operators to plan ahead for shutdowns and preventive maintenance of their furnaces.
Air Products has recently developed a dew point monitoring system to address these issues.
Read less…
Dew points of –35 to –45°C (–31 to –49°F) are typically desired in the hot zone to ensure carbon control and a good sinter. Continuous monitoring of the dew point in the hot zone can be challenging. Particulate and vapor-phase contaminants in the sample gas stream can potentially accumulate in filtering systems and on sensors. As a result, dew point readings can drift significantly, causing erroneous measurement and necessitating frequent cleaning, recalibration, and sensor replacement. Temperature variations within the sampling unit can also impact the accuracy of the sensors.
These issues can be mitigated by incorporating an automated self-cleaning and sensor calibration process. Temperature control of the sensor and the sampling system are also essential to maintain consistency. This can be achieved via various design features. Drifts and changes in dew point that are reported through local monitoring/alarms or remotely through cloud server access can also help to address furnace operational issues quickly and efficiently.
Continuous dew point monitoring helps manufacturers comply with CQI-9 and NADCAP requirements, and enables operators to plan ahead for shutdowns and preventive maintenance of their furnaces.
Air Products has recently developed a dew point monitoring system to address these issues.
Read less…
CONTINUOUS DEW POINT MEASUREMENTS SYSTEM FOR A SINTERING FURNACE
“Customers using our continuous dew point monitoring technology find
that the system enables uninterrupted use, without the need for
calibration or maintenance, and provides alerts on process drifts and
maintenance needs.”
Tom Philips, Applications Engineer
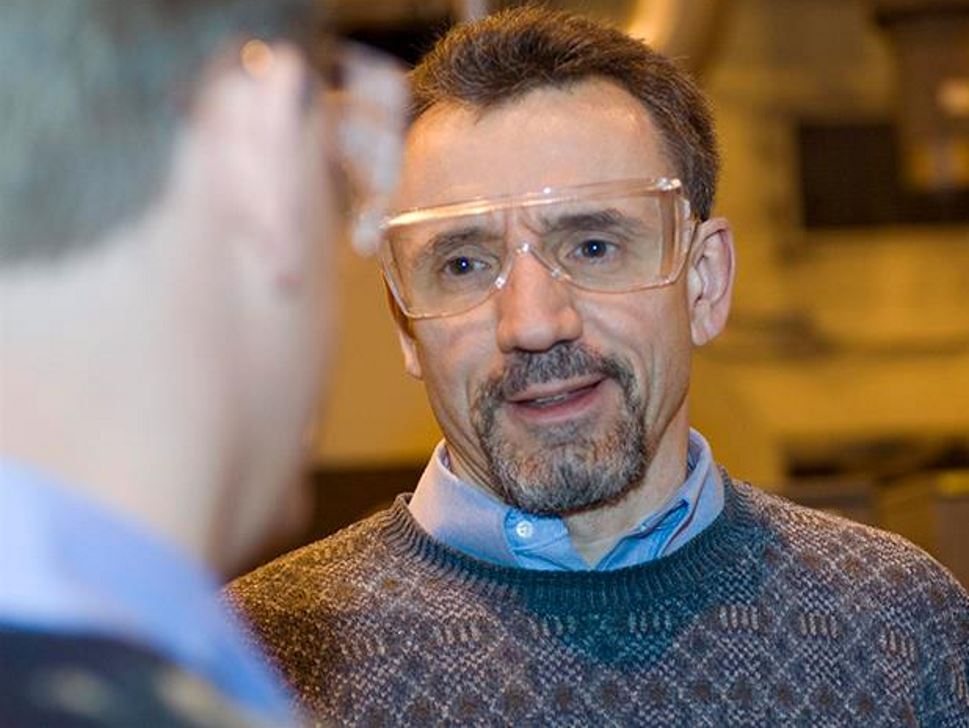
Industrial Gas Audits and Leak Detection Services
Audits and leak detection services can be comprehensive assessments of the entire gas supply system, or specific to gas or process equipment that use the gas.
Additional Services Contact us to help you enhance your furnace operations
Our industry experts apply their technical knowledge working with customers to find solutions that optimize performance and reduce cost.